History of GTRE.
In the early 1970s, GTRE had embarked on research projects in the area of compressor, combustor, turbine, engine control system, heat transfer,and so on, so that the input from these projects would provide valuable data for configuring a viable indigenous propulsion system. In the mean time,the work on the integration of the single-stage transonic compressor with six subsonic stages of the Orpheus 703 engine had been completed and the performance level achieved during the static tests in May 1974 proved the reliability, repeatability, and mechanical integrity of the design and gave considerable confidence to the GTRE team to take on the development of a power plant for the military aircraft
GTRE developed the reheated version of orpheus-703.
Eleven prototypes were built and extensive bench testing of over 2000 hr under extreme tropical conditions were also carriedout. The reheat engine Orpheus 703-1700K was fitted on a prototype of Marut and over 250 hr of flight testing were completed. These tests indicated that there was substantial improvement in performance by the Orpheus 703-1700K engine in respect of takeoff, run, climb, acceleration, maximum speed etc., over the non-reheat engine2,3. The Orpheus 703-1700K engine was type certified in December 1973.
Later on aircraft designers launched the Marut MK II design around the programm GTRE-developed Orpheus-703 reheat engine . Subsequently GTRE took up the design and development of Orpheus 703-2000 K reheat system. Two prototypes were built, successfully bench tested for about 160 hr and then subjected to simulated flight testing at the Altitude Test Facility in UK.
It was a pity that the crash of the redesigned Marut fitted with the reheat
engine in one of the early development flights put an end to the Marut Mk II
and the Orpheus reheat engine programme.
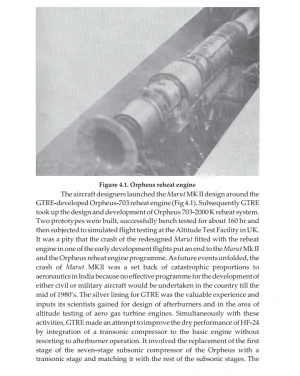
GTRE was also involved the replacement of the first stage of the seven-stage subsonic compressor of the Orpheus with a transonic stage and matching it with the rest of the subsonic stages. integrated research engine system was test run in May 1974 and the results were encouraging.
In 1974,GTRE embarked upon the programme of designing and developing an engine demonstrator programme based on a straight jet engine. The plan called for development of important subsystems incorporating latest technological advances for the demonstrator engine. The laboratory adopted the flat rating concept presently well known as high throttle ratio so that the configured engine system would be optimised at high forward speed and high ambient temperatures
A number of testing & manufacturing facilities were ser up.
Number of developments were done in the area of compressors and combustor.
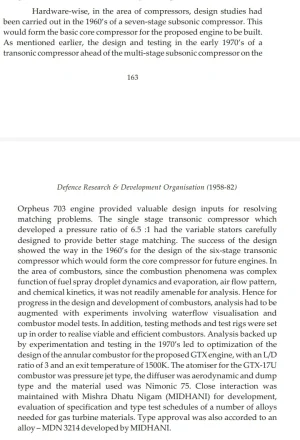
Similar developments were also done in the area of turbines.
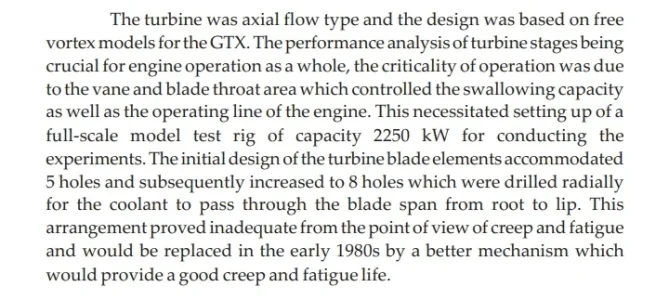
GTRE successfully addressed the issue of vibrations.
GTX incorporated all components /subsystems, such as transonic
compressor, annular combustor, shrouded cooled turbines, fully variable
exhaust nozzle, digital control system and sophisticated materials and
metal-forming techniques. The engine was test run successfully bringing to
an end the demonstrator phase of engine development..
In 1980, discussions were held between GTRE and M/s Rolls Royce of UK to examine the feature feasibility of developing a viable engine designated GTX-Adour which would integrate the core of the Adour engine used in the Jaguar with the components of GTX design. The collaboration did not materialise and it was decided to go ahead with the full-scale development of the GTX engine.This engine would serve as a highly effective and useful test vehicle for validating advanced technology design features
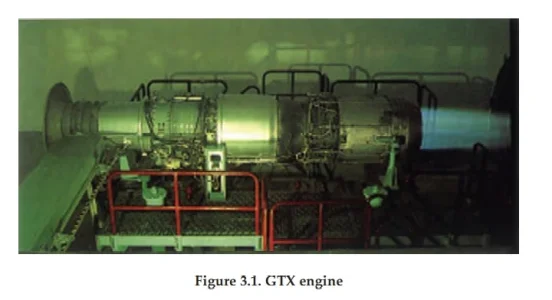